Noticias
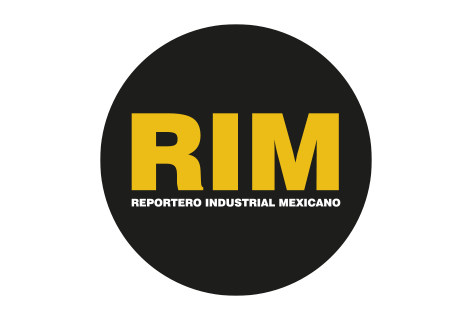
Los avances tecnológicos permiten ejercer un mejor control de la carga, así como la sincronización de elevación y antibalanceo, entre otras ventajas
La incorporación del IoT (Internet of Things o Internet de las Cosas en españil) al entorno industrial y de fabricación, concepto conocido como IIoT (Industrial Internet of Things o Internet Industrial de las Cosas) es, desde hace algunos años, uno de los conceptos más escuchados en las plantas industriales. Y no es para menos, pues la interconexión digital entre objetos ha permitido que las fábricas sean mucho más inteligentes, lo que ha provocado la reducción de costos y optimización de tiempos de producción, entre muchas otras bondades.
El IIoT asociado al Big Data, otra de las tecnologías vinculadas a la llamada Industria 4.0, también se ha convertido en una de las soluciones más socorridas dentro de las plantas productivas, pues esta asociación ha permitido recoger, almacenar, analizar y trabajar con datos dentro de las fábricas, lo que ha derivado en la evolución del mantenimiento preventivo al predictivo, además de que ha reforzado diversos esquemas de apoyo para la toma de decisiones.
Lea también: Automatización en México crecerá en 2022
En concreto, la interconexión masiva de sistemas, máquinas, herramientas y dispositivos periféricos, entre otros elementos, aunado a la compilación de datos para su análisis con el uso de algoritmos (Inteligencia Artificial), ha provocado el salto desde la tercera revolución industrial (computación y automatización) hacia la denominada cuarta revolución industrial (sistemas ciberfísicos).
El IIoT ha alcanzado a muchos de los procesos y herramientas utilizadas dentro de las plantas y no solo a las soluciones que se creía eran más susceptibles de evolucionar, como las máquinas-herramienta, los robots y en general todas las tecnologías utilizadas para la automatización.
Un caso emblemático de este fenómeno es el encontrado en las grúas industriales, una de las principales maquinarias utilizadas para el traslado de materiales, sobre todo dentro de sectores que requieren del traslado de cargas sumamente pesadas, como la industria manufacturera.
Aunque existen diversos tipos de grúas, una de las más utilizadas en entornos industriales es la viajera, que se distingue por su estructura colocada en el techo de las naves, desde donde se manipula la carga.
Por otro lado, las grúas móviles, también ampliamente usadas en las fábricas, se caracterizan por su buena habilidad de manejo, razón por la cual son utilizadas para tareas de traslado en lugares estrechos.
Otras grúas con aplicaciones en entornos industriales son la torre y la pluma. La primera es utilizada en tareas de elevación o distribución de cargas y destaca por su estabilidad, pues puede enclavarse en el suelo.
Con respecto a la segunda, esta se caracteriza por su capacidad para elevarse en sí misma y porque puede engarzarse con otras grúas a través de sistemas hidráulicos o mecánicos.
IIoT y grúas
Si bien el propósito de las grúas industriales continúa siendo el mismo –manipular cargas en entornos laborales–, la inclusión del IIoT en las plantas ha provocado que en la actualidad existan algunos fabricantes de grúas que, conscientes de esta evolución, se encuentren desarrollando soluciones asociadas al Internet de las Cosas.
Un ejemplo es la firma GH Cranes & Components, grupo que cuenta con más de 60 años de experiencia en el diseño y fabricación de grúas y polipastos, y que tiene entre su portafolio de soluciones el sistema CORE+, con el cual la compañía –en colaboración con Schneider Electric– logró dotar de inteligencia a una herramienta cuyo principio básico de funcionamiento se remonta a la antigua Grecia.
El CORE+ se basa en una pantalla táctil cuyo controlador, incorporado a la grúa, convierte a esta herramienta en una solución con múltiples funcionalidades que van desde la supervisión de la tarea hasta otras referidas al control de la carga, sincronización de elevación y carro, y antibalanceo de puente y carro.
Las multifunciones antes descritas son posibles gracias a que el CORE+ cuenta con una combinación de productos asociados al IIoT, como sensores y sistemas RFID, Megalis SCU, PLC de pantalla táctil y EcoStruxure Machine Advisor, soluciones desarrolladas por Schneider Electric.
Además, el sistema EcoStruxure Machine Advisor permite que la grúa reutilice hasta 40% de la energía utilizada por herramienta durante su operación, lo que sin duda representa una ventaja para los fabricantes.
CORE+ se puede integrar a diversos tipos de grúas con distintos variadores y motores; y desde su pantalla táctil es posible configurar y supervisar el estado de los indicadores más importantes de la herramienta, como el consumo eléctrico, alarmas y errores del sistema.
Funcionalidades
SYNCHRO, una de las funcionalidades de CORE+, es también un ejemplo de la evolución que las grúas y polipastos utilizados en entornos industriales han tenido en los últimos cinco años.
Según indica GH Cranes & Components en su blog, CORE+ SYNCHRO permite mantener, de forma automática, la distancia relativa entre dos ganchos –tanto horizontal como verticalmente– al utilizar dos polipastos, siendo esta su principal ventaja.
CORE+ SYNCHRO recibe continuamente de los variadores de frecuencia las siguientes entradas: Órdenes del operario (acelerar/decelerar), Velocidades reales (elevaciones, carros y grúa), Posición vertical de los ganchos (proporcionada por el encoder en los motores de elevación) y Distancia relativa horizontal entre carros (dada por el telémetro láser). Además, cuenta con un algoritmo que determina, basándose en las entradas mencionadas, las rampas óptimas de aceleración y desaceleración.
Por su parte, el CORE+ STABILITY, ideado para grúas puente, fue diseñado para facilitar el ensamble de piezas complejas. Concretamente, esta solución, según advierte el fabricante, reduce el efecto de balanceo producido por los movimientos de aceleración y frenado de la carga, por lo que es efectivo para los movimientos tanto del carro como de la grúa.
De igual forma, cuenta con una pantalla táctil de fácil configuración desde donde se puede supervisar el estado de la herramienta.
Lea también: Los desafíos en la industria manufacturera
Sobre cómo funciona, CORE+ STABILITY recibe continuamente de los variadores de frecuencia las siguientes entradas: Órdenes del operario (acelerar/decelerar), Velocidades reales (elevaciones, carros y grúa) y Posición vertical de los ganchos (proporcionada por el encoder en los motores de elevación).
Ahora bien, su algoritmo, basándose en las entradas mencionadas, determina las rampas óptimas de aceleración/deceleración para luego comunicar a los variadores de frecuencia cómo ejecutar el movimiento.
El arribo del IIoT a las plantas productivas continuará detonando la evolución de herramientas tan sofisticadas como los robots o las máquinas CNC, así como de herramientas utilizadas desde hace varios siglos, como las grúas.
Sin duda, la colaboración entre GH Cranes & Components y Schneider Electric ejemplifica el camino que está tomando el desarrollo de nuevas soluciones para el traslado de materiales hacia las plantas industriales modernas.
Otros artículos de interés
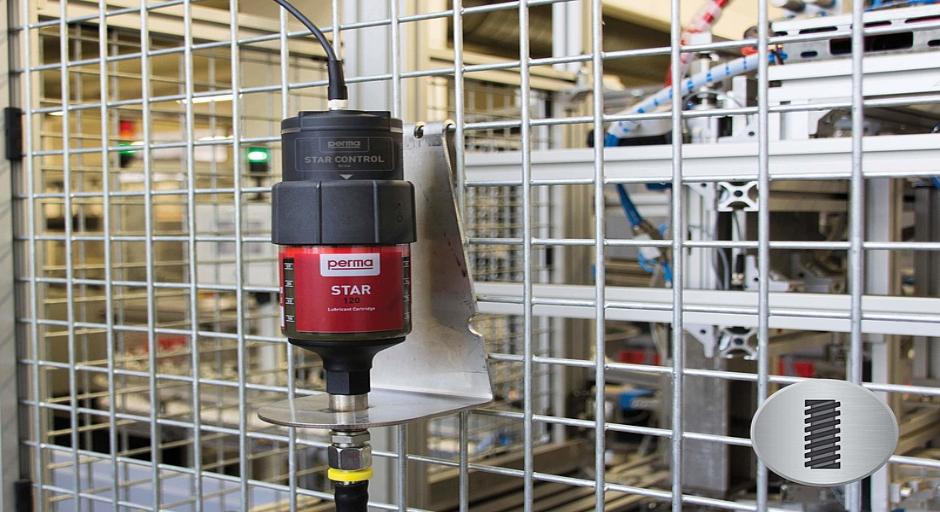
Lubricación automatizada, paso obligado en operación: Perma
En las plantas industriales, la lubricación ha pasado de ser una rutina
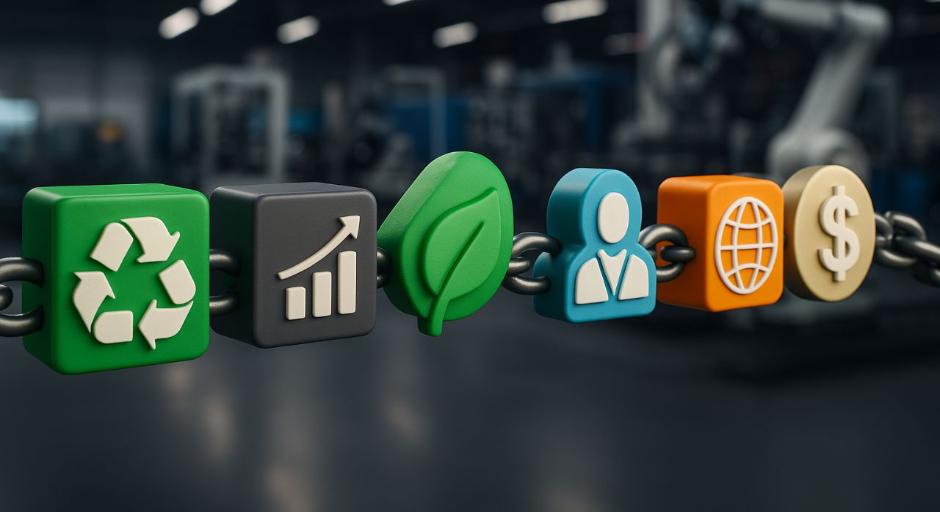
Cuidado ambiental: responsabilidad eslabonada
El cumplimiento de políticas de sostenibilidad en la industria manufacturera se ha
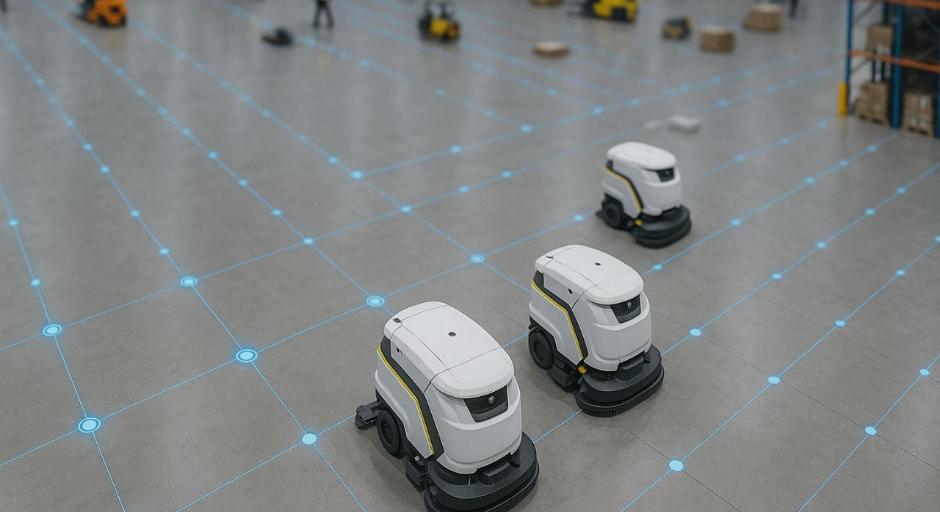
Limpieza industrial no escapa de la automatización
En la industria, la limpieza de áreas productivas es tan importante como

Suministro ininterrumpido para la Industria 4.0
La Industria 4.0 representa un salto evolutivo en la manufactura: sistemas físicos,
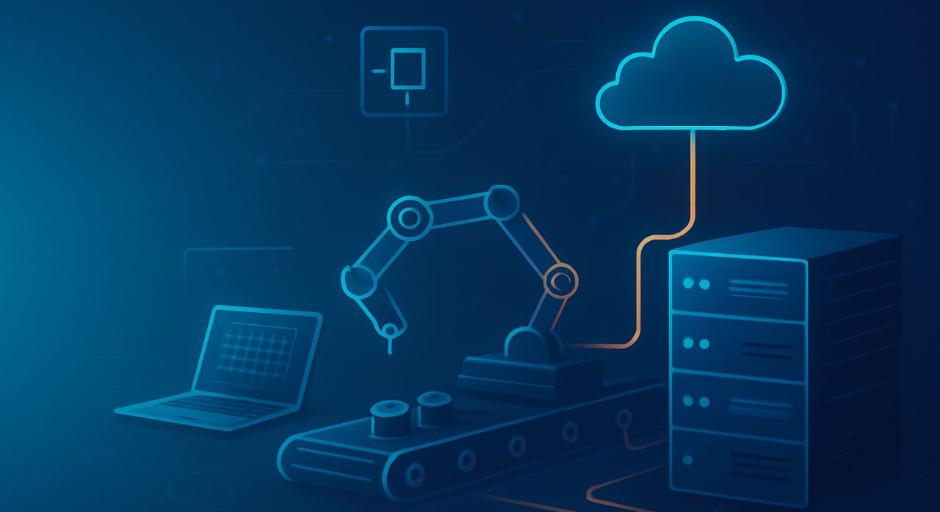
Por qué la manufactura requiere una buena infraestructura de redes
Con la adopción de tecnologías digitales en la manufactura, la infraestructura de

Transporte multimodal gana valor en la industria
En la industria manufacturera mexicana, la logística ha dejado de ser un